Fanuc Robodrill
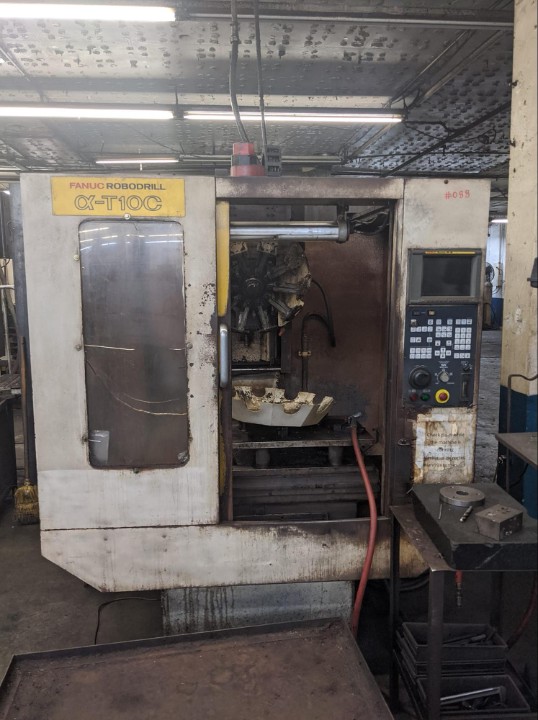
FANUC RoboDrill a-T10c Ballscrew Guys serviced a few weeks ago. Notice the layers of dirt, crud, grease, and solidified cutting fluid all over the outside of the machine. Gives the viewer a sample of what we found inside. We fully understand that many of these machines are used hard over the decades. They are work horses. Very handy for any fabrication facility looking to poke a hole in a part and tap it. Many of these machines don’t receive much love, let alone regular lubrication on a preventative maintenance schedule, The most common problem we have found with these machines is that the Z-Axis becomes loose and sloppy. Because it is a gravity assisted axis, many operators do not know their Z-Axis ball screw is about to die before it is too late.
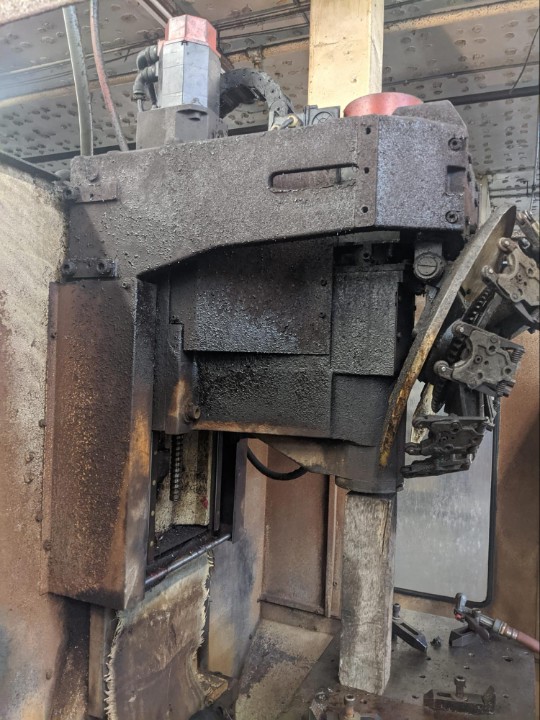
Side Panel removed from a FANUC RoboDrill. Notice the decades old layers or hardened cutting fluid and dirt. Accented by imbedded metal shavings. Destroyed ribbon covers are an added bonus. Even with all these cosmetic issues, this machine can be brought back into production, For the complete Z-Axis CNC motion system to be refurbished, all of this would have to be cleaned up. The debris and dirt must be removed before replacing new linear way guide rails, slide block bearing guides, and reinstalling the refurbished ball screw. If your machine needs service and looks like this, we may need to budget in man hours for machine cleaning.
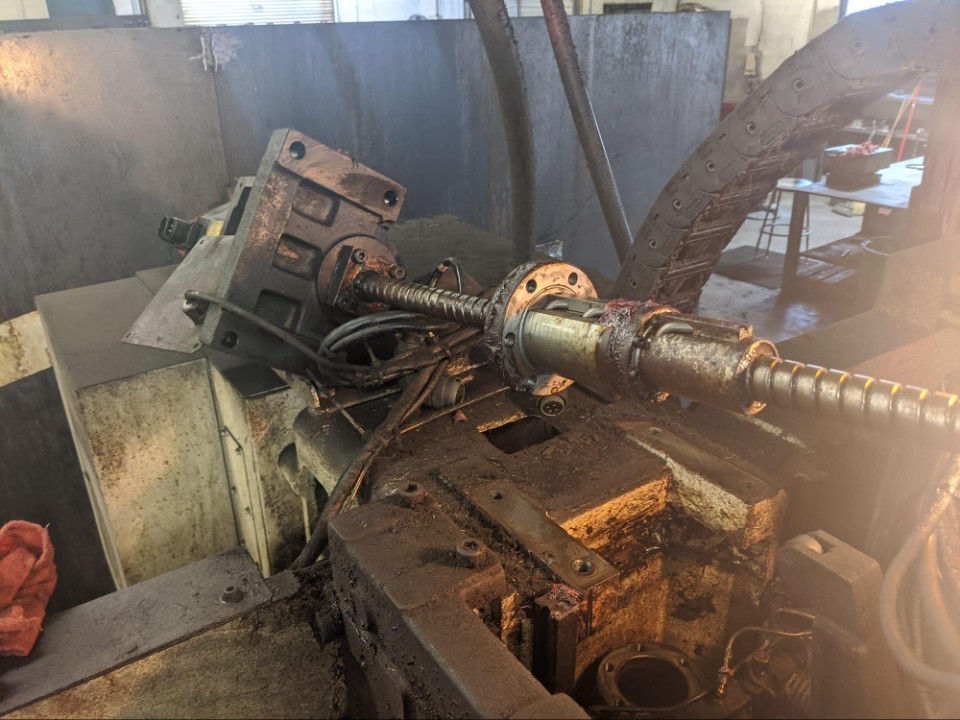
The entire Z-Axis ball screw and servo motor assembly pulled out of the top of a FANUC RoboDrill. This system was reported to have over 0.050” of slop and play in the ball screw. When moved in one direction, it would occasionally bind up, causing a torque alarm in the controller. Upon removal, disassembly, and cleaning of the ball nut we discovered the problem. One of the ball bearing recirculation tubes was damaged. It had a scoop shape formed on the end which had sheared off.
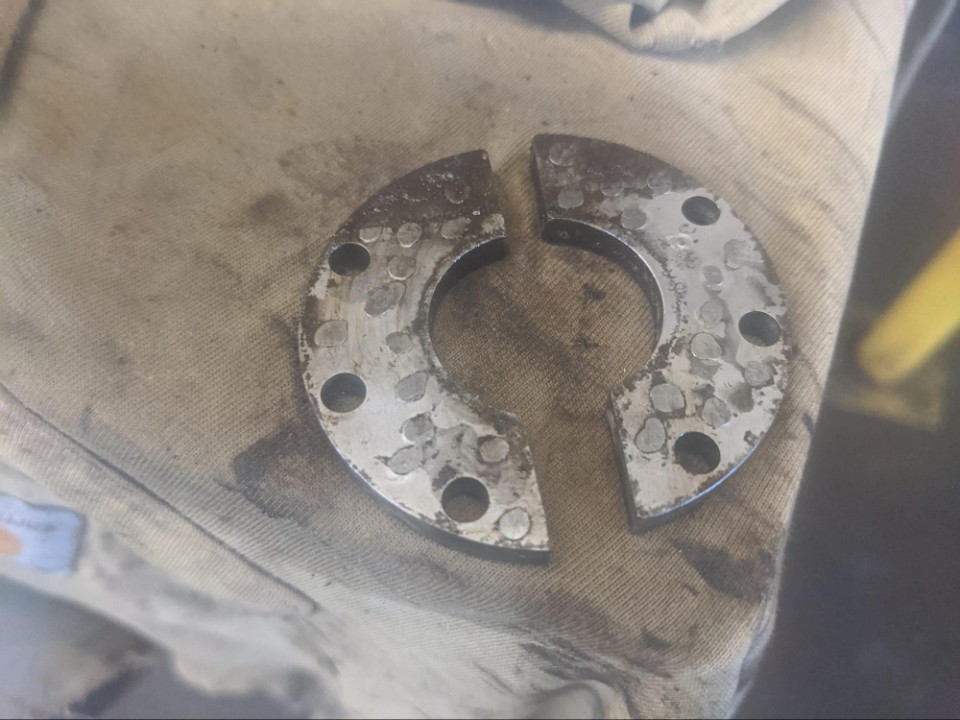
This is a spacer set from a FANUC Z-Axis ball screw assembly. Notice the blotches of material on the shims. These are tack welds made onto the shim. Then the shim was placed onto a surface grinder to make them uniform in thickness. We jokingly refer to this in the industry as a ghetto-fix. When thicker shims are placed inside a ball screw ball nut which breaks into two halves, it forces the two halves farther apart. This is a short term fix which works if you have worn ball bearings inside. But in reality you are increasing the rate in which the worn balls inside deteriorate. Risking permanent damage to the inside of the ball nut. This technique of increasing the spacer size is also sometimes used when someone attempting repair only has access to standard size ball bearings.Off the shelf. Ball screwGuys does not have this issue, as we strive to custom fit an oversized ballbearing to match the ball raceway wear exactly. No need to change the ball nut geometry if you have the right ball bearings that fit.